Getting round holes on support <Solved>
Getting round holes on support <Solved>
I've been dialing in my support settings for ABS builds, and I've made some good progress. The current optimum is .225mm layer, 1 layer separation top and bottom. I'm using 3 layers of dense support at 100%.
Bridging extruder multiplier 175% (might back down a touch)
Bridging speed multiplier 75% (I'm not bridging, just using these for the first layer on above the support)
I'm getting an even, fairly dense first layer on top of the support which separates cleanly with only a bit of stress whitening - a little time in an acetone sauna would clear that up, i'm sure. The only real issue is that where I have holes starting on support, they look like this: The hole is 6mm. There's a 1mm fillet around the edge of the hole. Haven't tried a build without the fillet.
I haven't stumbled onto anything that will give me a good outline around the first holes.
Looking at some parts from Makergear, they look very clean on the underside, and circular outlines are circular.
Any tips on how to make a round hole round?
Cooling has had a fan override of 100% for bridging. Trying one now at 25%.
Bridging extruder multiplier 175% (might back down a touch)
Bridging speed multiplier 75% (I'm not bridging, just using these for the first layer on above the support)
I'm getting an even, fairly dense first layer on top of the support which separates cleanly with only a bit of stress whitening - a little time in an acetone sauna would clear that up, i'm sure. The only real issue is that where I have holes starting on support, they look like this: The hole is 6mm. There's a 1mm fillet around the edge of the hole. Haven't tried a build without the fillet.
I haven't stumbled onto anything that will give me a good outline around the first holes.
Looking at some parts from Makergear, they look very clean on the underside, and circular outlines are circular.
Any tips on how to make a round hole round?
Cooling has had a fan override of 100% for bridging. Trying one now at 25%.
Last edited by zemlin on Mon Jun 20, 2016 2:11 am, edited 1 time in total.
- Matt_Sharkey
- Posts: 347
- Joined: Mon Oct 20, 2014 3:10 pm
Re: Getting round holes on support
Are you printing from the inside out? If the threads don't have enough to grab onto, they tend to make that pattern of the shortest path.
Re: Getting round holes on support
Printing inside out.
Reduced cooling did not make the circles round.
I did make the support more difficult to break off, but not too bad.
Reduced cooling did not make the circles round.
I did make the support more difficult to break off, but not too bad.
Re: Getting round holes on support
Holes on top of support is a problem because there is usually a single layer gap between support and the part. With that gap, tight arcs will tend to cut the corner because they don't grab onto the support before being pulled sideways.
If this is your own model, try making any such hole polygonal, at least for the interface layer.
If this is your own model, try making any such hole polygonal, at least for the interface layer.
Re: Getting round holes on support
Try removing that 1mm filet on the holes if you don't need it. Filets on the underside always wind up a little wonky, even with support under them. 

Re: Getting round holes on support
I ran one last night with the bridging speed multiplier down to 10% - that didn't make any difference.
Running one with sharp corners now, although i don't expect that to be an improvement either and the 3.5mm holes at the bottom of that counterbore don't look any better without a fillet. Extruder temp is 245 which seems to be working fine for the rest of the build. I can imaging that a higher temp, less viscous material, might pull less when laying down that first layer - might try that next.
Running one with sharp corners now, although i don't expect that to be an improvement either and the 3.5mm holes at the bottom of that counterbore don't look any better without a fillet. Extruder temp is 245 which seems to be working fine for the rest of the build. I can imaging that a higher temp, less viscous material, might pull less when laying down that first layer - might try that next.
Re: Getting round holes on support
So I was able to watch it build that first layer on my current attempt and noticed that the fan when high ONLY when doing the infill - so apparently the outlines are not considered bridging and all the adjustments I've been making to extrusion multipliers and speeds haven't changed anything, which would explain why all the parts look the same in that regard - so it seems there's not much I can do to resolve the issue as I don't have any control of the outlines for the first layer - only the infill.
I guess I'll set the bridging extrusion multiplier to 100% and decrease layer thickness a bit to see if I can hit a sweet spot rather than relying on the multiplier to accomplish anything.
I guess I'll set the bridging extrusion multiplier to 100% and decrease layer thickness a bit to see if I can hit a sweet spot rather than relying on the multiplier to accomplish anything.
Re: Getting round holes on support
On the Other tab there is a setting for Outline Underspeed - try changing that one to 50% or so. (Jin's right though - there is only so much you can do with a circular outline over a gap. Changing the Upper Vertical Separation to zero layers will improve the circle, but make it a nightmare to remove the support.zemlin wrote:So I was able to watch it build that first layer on my current attempt and noticed that the fan when high ONLY when doing the infill - so apparently the outlines are not considered bridging and all the adjustments I've been making to extrusion multipliers and speeds haven't changed anything, which would explain why all the parts look the same in that regard - so it seems there's not much I can do to resolve the issue as I don't have any control of the outlines for the first layer - only the infill.
I guess I'll set the bridging extrusion multiplier to 100% and decrease layer thickness a bit to see if I can hit a sweet spot rather than relying on the multiplier to accomplish anything.

Re: Getting round holes on support
I already run the outline underspeed quite low to improve outer surface quality - and BTDT with zero layersJules wrote:On the Other tab there is a setting for Outline Underspeed - try changing that one to 50% or so. (Jin's right though - there is only so much you can do with a circular outline over a gap. Changing the Upper Vertical Separation to zero layers will improve the circle, but make it a nightmare to remove the support.

It is what it is, but I'm not defeated yet.
Re: Getting round holes on support
Because the printer builds the object from uniform slices, the separation between vertical features must be multiples of the slice thickness. You might be able to gimmick up a smaller separation by changing the layer thickess in mid-object, but that way lies madness.zemlin wrote:absolute dimensions as an option on separation distance rather than full layers thicknesses
For little features like that, perhaps DIY support structures would work better. Here's the inside of a hexagonal recess for a 6-32 nut, done in PETG:
https://softsolder.com/2016/02/10/vacuu ... e-sockets/
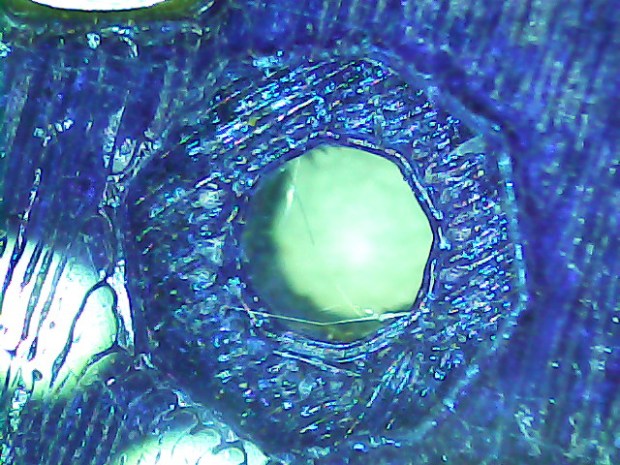
The support structures pressed out cleanly:

That has one empty layer between the support and the overhang. The legs on the support spiders are two threads wide and 90% of the recess diameter long.
The model shows how they fit together:

I set Slic3r to produce the perimeter threads last, at a relatively slow speed, and they stick firmly to the surrounding threads.
That won't solve the problem of supporting a tapered hole, though. If that's for a flat-head screw, perhaps you can fake a taper from a two or three cylindrical steps: the edges would crush when you tighten the screw.